We have motors!
(Chris)
Motors have been a massive bone of contention in the ARC team. Rob wants the most powerful motors he can find…. Chris wants ones he can actually find speed controllers for…. and Ali… doesn’t really care – as long as the robot goes in a straight line!
We settled (quite some time ago) on some motors from Alien Power Systems, and, we’ll be honest, they looked like they would do the job just fine…. assuming they ever arrived. Well, finally, 1 PayPal claim and a month and a half later, a parcel arrived at Rob’s with a pair of nice shiny motors in it. Can’t wait to fit them to the robot and get it moving!
(Rob)
Now, a little more detail about these motors – they are Alien Power Systems C8085’s, and, according to the Alien website, have a rated power of 6000W. Well, that’s not quite right. With no small amount of Googling, it turns out that these C8085’s are practically identical to the EMP and Turnigy motors of the same size, even so far as to be made in the same factory, and actually have a peak rating of 6150W, but a constant rating of either 4250W or 5110W, depending on which site you end up on.
If we ever need more of these motors (hopefully, we won’t burn them out!) we’ll be ordering them directly from China through The Quick Model Company.
Now that that’s out of the way, let’s talk about the motors themselves.
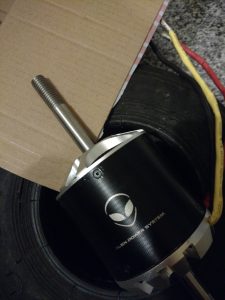
That big ol’ axle needs to go.
In short, they’re large. As Chris has alluded to above, originally I wanted to go with hugely powerful brushed motors, although he’s managed to talk me out of that by scaring me with the costs of the motor controllers. However, for our uses, they need a bit of modification – namely the removal of the large protruding axle shaft at the back (front?) of the motor, which causes us some problems. The best way of doing this would be to get to a lathe, remove the axle from the motor, mark it up and mill it down to size. Due to time constraints and the lack of a lathe, we’re going to go the slightly more maverick route and use the trusty metal cutting bandsaw that is in the workshop, and then cleaning up the edges of the protruding axle with some sandpaper. In order to protect the motor while we’re doing this, they will be wrapped in foam and the holes will be covered up with masking tape. The plan is to go very slowly with cutting fluid and hope that it works.
When we are next in the shop, we’re also going to be checking our drive pulleys to make sure that the “M3” (I’m not convinced) grubscrew is the same as the 3mm keyway that’s on the other side of the axle.